摘 要
孔道壓漿作為后張法預應力混凝土梁結構施工工藝中不可或缺的環(huán)節(jié)之一,它對于預應力筋正常發(fā)揮和預應力筋的保護起著至關重要的作用。其質量的好壞也直接影響著后張法預應力混凝土結構的安全性和耐久性,現如今,孔道壓漿的發(fā)展得到了眾多學者和工程界人士的廣泛關注與重視,所以探討與研究性能優(yōu)異的壓漿料是具有現實應用價值的。 參照《鐵路后張法預應力混凝土梁管道壓漿技術條件》中對壓漿料的要求,并針對目前現有壓漿料存在的流動性差及早期強度低等問題,研究了高效聚羧酸減水劑及早強劑對壓漿料性能的影響,結果表明,選擇與水泥適應性良好的高效聚羧酸減水劑能改善壓漿料的流動性,使其初始流動度和30min流動度分別控制在20s和30s內;摻入甲酸鈣作為早強劑,可以提高壓漿料的強度。在此基礎上,采用消泡劑和改性劑對壓漿料的性能進行改善,優(yōu)化了配合比,確定了各個組分的較適宜摻量范圍。 在分別確定各組分的最佳摻量后,通過試驗優(yōu)化得到壓漿料的最佳配合比例為:水泥79.5%,粉煤灰15%,減水劑1.0%,早強劑2.5%,消泡劑0.2%,改性劑1.8%,根據優(yōu)化后的配合比制得的壓漿料流動性良好,無泌水離析現象,7d和28d抗壓強度分別達到45MPa和60MPa以上,表面光滑無氣孔,壓漿料的綜合性能優(yōu)異。 1 緒論 1.1 課題背景 目前國內鐵路的高速發(fā)展,預應力混凝土發(fā)揮了其他混凝土不可比擬的作用,根據設計、制作及施工工藝的不同,預應力筋分為先張法和后張法兩種。目前我國高速鐵路大跨度橋梁中懸臂施工,現場澆筑等大型工程構件多采用后張法預應力混凝土,后張法預應力混凝土梁結構施工工藝里面最為重要、最為關鍵的工藝環(huán)節(jié)就是孔道壓漿,首先它能夠保護預應力筋,使其不被銹蝕,還能夠使其與混凝土良好地結合在一起,使預應力的有效傳遞得到保證。再者,孔道壓漿可以讓預應力鋼筋和混凝土完美結合、共同工作,這極大地提高了結構的可靠度和耐久性。所以壓漿料質量的優(yōu)劣對后張法預應力的安全性和耐久性有非常重大的意義??椎捞畛渌枰墓酀{材料需要具備早強、高強、高流態(tài)、不泌水和無收縮這幾個基本特征。但是傳統(tǒng)管道壓漿施工方法中用的普通的灌漿材料存在這強度、流動性差,泌水,干燥收縮出現裂縫等缺陷;而且還會出現早強與和易性差、流動度與密實度之間的矛盾,因此,如何得到具有良好和易性、早強、高強、無收縮等多種優(yōu)點的壓漿料,成為本領域技術人員亟待解決的技術問題。 1.2 課題目的與意義 國內高速鐵路的建設正處于飛速發(fā)展的時期,能夠讓混凝土和預應力筋結合起來、共同工作,并能使預應力得到有效傳遞和不被腐蝕,孔道壓漿的作用就顯得如此的不可或缺。但是預應力結構質量問題仍然在實際生產中屢見不鮮,或是因為專業(yè)人員的技術不足,或是施工管理相對滯后,又或是監(jiān)督措施不完善等。因此,為了解決預應力結構構件在施工中存在的問題,需要首先對壓漿料進行改善。后張法預應力是一種張拉預應力筋以形成預應力混凝土構件的施工方法,其需要先澆筑水泥混凝土,等到混凝土達到設計強度的75%以上時再進行張拉預應力筋。它與先張法預應力混凝土的主要區(qū)別是:先張法是將張拉后的預應力筋直接澆筑在混凝土內,依靠預應力筋與周圍混凝土之間的粘結力來傳遞預應力;后張法預應力混凝土的預應力筋則需要徹底借助端頭錨具來實現傳遞壓力。與普通混凝凝土對比,后張法預應力混凝土具有無可比擬的優(yōu)勢;在相同的條件下,后張法預應力混凝土不僅具有構件截面小、質量好以及自重輕等優(yōu)點,而且大幅度提高了建筑結構的抗裂性能和耐久性能??傊?,用后張法預應力混凝土結構來代替普通鋼筋混凝土結構在結構跨度較大的情況下是十分具有可行性的。 通過查閱相關文獻資料及工程實踐發(fā)現,大多數的灌漿材料存在這強度、流動性差,泌水,干燥收縮出現裂縫等缺陷;而且還會出現早強與和易性差、流動度與密實度之間的矛盾。本課題旨在研究一種孔道壓漿料,使其與水泥按一定比例配合后,滿足鐵路預應力混凝土梁孔道壓漿的技術要求。通過試驗方法測試摻入摻合料的的孔道壓漿料的工作性能、物理性能和耐久性,發(fā)現優(yōu)化配合比后的孔道壓漿料按一定比例與水泥混合后,不僅能增加混凝土早期強度和后期強度,而且改善了混凝土的流動性與密實性等問題。從而減輕了預應力混凝土的破壞,延長使用壽命,具有重大意義。 1.3 國內外研究現狀 在2008年之前國內關于孔道壓漿的規(guī)范TB/T3192-2008《鐵路后張法預應力混凝土梁管道壓漿技術條件》尚未頒布,我國工程建設對于預應力結構的安全性、耐久性的要求以及對于孔道壓漿的重視程度就已經隨著我國經濟的快速發(fā)展和鐵路的基礎建設日益地提高,之前的規(guī)范在壓漿材料的控制方面所涉及到的指標少之又少,以至于壓漿材料的性能不能夠精準地被控制。作為我國國內要求較為全面的也是最早的孔道壓漿規(guī)范TB/T3192-2008《鐵路后張法預應力混凝土梁管道壓漿技術條件》的頒布與實施,在對泌水率提出更高要求的基礎上還補充了對于流動度的要求(主要指標如表1.1所示)。該規(guī)范不僅涉及到對耐久性等性能的要求,同時還使孔道壓漿材料的試驗標準方法得要了進一步的完善。TB/T3192-2008《鐵路后張法預應力混凝土梁管道壓漿技術條件》在技術方面的嚴格要求了水膠比和工作性能以及明確規(guī)定了攪拌的速度,這也是國內迄今為止對鐵路系統(tǒng)孔道壓漿材料指標最為嚴格的要求、技術要求最為全面的規(guī)范文件。 表1.1 TB/T3192-2008對預應力孔道壓漿料的技術要求
表1.2 PTI規(guī)范和FDOT規(guī)范的性能指標對比
國外對預應力技術使用較早也更為成熟,對孔道壓漿的研究更為深入,現今國外關于孔道壓漿材料比較先進的技術規(guī)范主要有兩個,其一是美國后張預應力協(xié)會發(fā)布的《Specification for grouting post- tensioned structures》,其二是佛羅里達發(fā)布的《Standard Specification for Road and Bridge Construction 2007 》,兩個規(guī)范均以ASTM為標準來測試各項性能指標【10.11】,這兩個規(guī)范具體要求了孔道壓漿材料的耐久性、穩(wěn)定性、流動性、泌水率、強度等指標(完整技術指標規(guī)定對比如表所示),同時,這兩個規(guī)范也是迄今為止國外在壓漿材料方面有較為全面和系統(tǒng)的技術性能指標規(guī)定的規(guī)范。由表1.2中可以看到,這兩個規(guī)范的指標全面中帶有側重,例如膨脹率與總氯離子含量在兩個規(guī)范中都沒有做出相關規(guī)定,但是弗羅里達對于體積穩(wěn)定性的要求更為嚴苛,所以,就全過程規(guī)定而言,前者的范圍較為狹窄,后者的規(guī)定就更為全面。 1.4 本課題的研究內容 高速鐵路大跨度橋梁等大型工程構件多采用后張法預應力混凝土,其孔道的填充需要高流態(tài)、早強、高強、不泌水、無收縮的灌漿材料。而普通的灌漿材料存在著強度、流動性差,泌水,干燥收縮出現裂縫等缺陷;而且還會出現早強與和易性差、流動度與密實度之間的矛盾,因此,如何得到具有良好和易性、早強、高強、無收縮等多種優(yōu)點的壓漿料,成為本領域技術人員亟待解決的技術問題。本課題旨在研究一種孔道壓漿料,使其與水泥按一定比例配合后,滿足鐵路預應力混凝土梁孔道壓漿的技術要求。具體研究內容如下: 1、孔道壓漿料各組分的適應性研究:減水劑、早強劑、摻合料等; 2、孔道壓漿料配合比的優(yōu)化設計;主要優(yōu)化其他功能組分; 3、孔道壓漿料與水泥配合后,壓漿料的各項性能指標測試,并進行優(yōu)化調整。 2試驗原材料及試驗方法 2.1 原材料 2.1.1 水泥 水泥作為壓漿材料里最為普通也最為重要的組分之一,其品種的不同、強度等級的高低和用量的多少等無一不影響著壓漿材料的質量。水泥在后張預應力孔道壓漿的應用應符合《通用硅酸鹽水泥》GB175所規(guī)定的技術要求、適用范圍以及對低堿硅酸鹽或低堿普通硅酸鹽的限制?;诖?,本實驗水泥采用湖北某水泥企業(yè)生產的P.O42.5級水泥。其主要化學成分和性能指標分別見表2.1、表2.2。 表2.1 原材料的化學成分(質量份數%)
表2.2水泥的物理力學性能
2.1.2 粉煤灰 粉煤灰采用武漢陽邏電廠的II級粉煤灰,其化學成分見表2.1。 2.1.3 減水劑 減水劑采用華軒高新的粉狀PC-303型聚羧酸減水劑。 2.1.4 其他功能材料 消泡劑采用有機硅類消泡劑。 早強劑選用市售工業(yè)級甲酸鈣,有效含量大于92%。 2.1.5 拌和水 實驗用拌和水選用飲用自來水。 2.2 試驗方法 參照《鐵路后張法預應力混凝土梁管道壓漿技術條件》規(guī)定的實驗方法。 3 孔道壓漿料的性能研究 3.1 孔道壓漿料基本組分研究 后張預應力梁壓漿材料一般需要混合一定比例的高性能壓漿料和水泥并摻入一定量的水攪拌來制成。在配制壓漿材料時一般還需要加入一定量的外加劑和摻和料來滿足其流動性、抗泌水性和膨脹性等性能的要求。有時因為水泥本身流動性的不足而人為過分地提高水膠比會影響和破壞孔道壓漿材料的物理和耐久性能。在這種情況下,加入減水劑的方法就應運而生,它不但可以保持較低的水膠比,而且還能保證較好的水泥流動性。第一步應當是粗選減水劑、粉煤灰和硅灰的摻量,第二步則是對減水劑、粉煤灰和硅灰摻量以及水膠比展開試驗來探究各組分對壓漿材料影響,接著便是探究微膨脹劑、消泡劑和緩凝劑對壓漿材料物理力學和工作性能的影響,最后通過上述試驗來得到壓漿料的最優(yōu)配比。 3.1.1 減水劑適應性實驗 表3.1 PC-303減水劑對壓漿料流動度的影響(粉煤灰摻量15%)
圖 3.1 PC-303減水劑對壓漿料初始流動度的影響
圖 3.2 PC-303減水劑對壓漿料30min流動度的影響
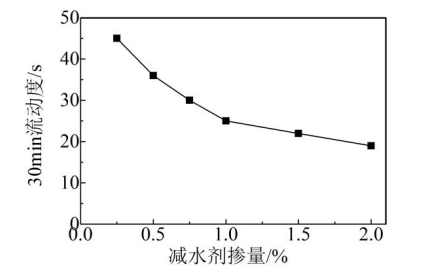
減水劑通過吸附在水泥顆粒的表面來分散之前水泥顆粒形成的絮凝結構,以達到有效增大壓漿材料流動性能的目的。許多研究均指出,對水泥水化起緩凝作用的是減水劑,水泥的硬化過程可以靠減水劑的作用來一定程度地放緩,與此同時,水化產物的體積、空間分布以及阻止水泥顆粒的絮凝均可以依賴減水劑的作用,由此可見,減水劑對于保持壓漿材料的流動性有著非凡的意義。減水劑除了能夠保持流動度還能降低水膠比,減水劑這一功能為提高壓漿材料的抗腐燭和結實度性能創(chuàng)造了條件。向水泥漿體加入高效減水劑是有一個臨界點的,一旦超過這一臨界摻量,水泥裝體的流動性就不會再隨減水劑加入量的增加而增加,我們把這個臨界點稱之為飽和點,飽和點下的減水劑加入量被稱之為飽和摻量。試驗將采用水膠比、通過水泥凈架的試驗來對減水劑與水泥的適應性進行測試,以此而確定減水劑的一個合適的摻量范圍。本試驗不同減水劑摻量對壓漿料流動性的影響結果如表3.1和圖3.1、圖3.2所示。 由圖中可知,減水劑對壓漿材料的流動性影響顯著,隨著減水劑摻量的增大,流動時間縮短,流動度增加,當摻量達到0.75%時,初始流動時間為23s,接近標準要求的22s以下,其30min的流動時間為30s,已經達到標準要求。當減水劑摻量繼續(xù)增大到1.0%時,初始流動度和30min流動均在標準要求的范圍內。再增加減水劑的摻量時,流動時間繼續(xù)縮短,但減水劑摻量過大容易造成漿體泌水,在試驗過程中發(fā)現,當摻量達到1.5%時,有輕微泌水的現象,當摻量為2.0%時,泌水情況嚴重,所以確定減水劑的最佳摻量為1.0%。 3.1.2 摻入粉煤灰分析 孔道壓漿材料對其工作性能具有較高的要求,研究表明:粉煤灰替代部分壓漿材料中的水泥,不僅能夠提高壓漿材料的流動性能,而且由于粉煤灰的比表面積比水泥大,還能夠降低漿體的泌水率和沉降作用,粉煤灰顆粒填充水泥顆粒的空隙可以提高壓漿材料的后期強度和抗化學侵燭能力并能使壓漿材料保持良好的體積穩(wěn)定性。 粉煤灰的形態(tài)特點包括顆粒表面光滑、粒度較細,大量含有玻璃微珠,顆粒密度也均小于水泥顆粒,這些特點不僅能使?jié){體的體積增加,而且能夠在保證水膠比不變的前提下明顯改善漿體的流動性。此外,粉煤灰顆粒填充到水泥顆粒的空碩士學位論文孔道壓裝材料優(yōu)化配伍隙中,改善了漿體的顆粒級配,對于減小裝體的分層離析的現象具有很好的效果,所以本文研究過程中摻入15%的粉煤灰等量替代水泥。 3.1.3 早強劑對壓漿料性能影響 壓漿料的流動性大,導致水泥水化時水分過多,這可能會影響壓漿料的強度發(fā)展,所以為了能提高壓漿料的早期強度,并且對后期強度無顯著影響,在壓漿料的配合比中加入早強劑。本文在研究過程中選用早強效果較好的甲酸鈣作為早強劑,早強劑對壓漿料的凝結時間和力學性能影響見表3.2、圖3.3-圖3.5。其中減水劑的摻量為1.0%,粉煤灰的摻量為15%。 表3.2早強劑對壓漿料性能的影響
由圖3.3不同甲酸鈣摻量時壓漿料的凝結時間數據可以看出,摻入甲酸鈣后,有利于壓漿料凝結時間的縮短,而且隨著甲酸鈣摻量的增加,壓漿料終凝時間的縮短幅度要大于初凝時間的縮短幅度,即早強劑甲酸鈣可以縮短壓漿料初凝時間和終凝時間的時間間隔。當甲酸鈣的摻量達到3.0%時,壓漿料的凝結時間降低到3小時40分鐘,不滿足標準中對壓漿料的凝結時間要求了,所以早強劑甲酸鈣的摻量不能大于2.5%。摻入不同比例甲酸鈣的壓漿料的終凝時間均在24小時以內,各摻量的終凝時間均滿足標準要求。 圖 3.3 甲酸鈣對壓漿料凝結時間的影響
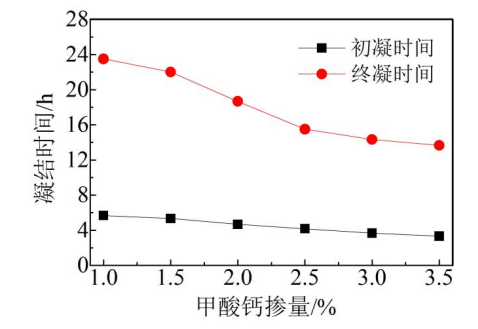
圖3.4為不同甲酸鈣摻量情況下壓漿料的7d和28d抗折強度。由圖中可以看出,隨著甲酸鈣摻量的增加,壓漿料的7d抗折強度呈先增大后減小的趨勢,在摻量小于3.0%時,甲酸鈣有助于壓漿料7d強度的發(fā)揮,但是當摻量大于3.0%時,7d抗折強度略有降低。這是因為,加入甲酸鈣后,促進了水泥的早期水化反應,使抗折強度增加,但是當摻量過大時,由于早期水化速度過快,迅速產生的水化產物部分覆蓋了未水化的水泥顆粒,導致水泥的水化度降低,從而使抗折強度降低。壓漿料28d的抗折強度規(guī)律同7d的變化規(guī)律相似,說明,加入適量的甲酸鈣也有助于壓漿料后期強度的發(fā)揮。 圖 3.4 甲酸鈣對壓漿料抗折強度的影響
圖 3.5 甲酸鈣對壓漿料抗壓強度的影響
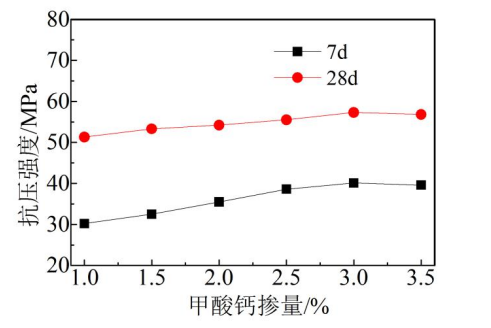
圖3.5為不同甲酸鈣摻量情況下壓漿料的7d和28d抗壓強度。由圖中可以看出,甲酸鈣對壓漿料抗壓強度的影響規(guī)律同抗折強度相似,表明在一定摻量范圍內,甲酸鈣有助于壓漿料抗壓強度的發(fā)揮。 綜合考慮甲酸鈣對凝結時間和力學強度的影響,并參照標準的要求,確定壓漿料中甲酸鈣的摻量為2.5%。 3.2 孔道壓漿料配合比優(yōu)化 在進行壓漿料基本組分研究過程中,發(fā)現攪拌出的壓漿料漿體存在氣泡,且凝結硬化后的壓漿料試塊的表面和內部存在很多大的氣孔,這會嚴重影響壓漿料的力學性能和耐久性能。而且水泥基材料體系在凝結硬化過程中會產生收縮現象,所以采用一些其他功能組分對孔道壓漿料的配合比進行優(yōu)化,從而改善壓漿料的性能。 3.2.1 其他功能組分 通過加入消泡劑的方式降低壓漿料漿體中的氣泡,降低凝結硬化后的試塊的氣孔率。消泡效果較好的有機硅類消泡劑的選用,能使其在壓漿料漿體表面的鋪展簡單迅速,然后快速并自動地分散于氣泡表面,吸走鄰近的一層表面溶液是的液膜厚度變薄,液膜厚度達到破裂的臨界的液膜厚度時氣泡就會破裂,這就起到了減少空隙的作用。本實驗根據文獻和前人的研究確定有機硅類消泡劑的摻量為0.2%。 由于壓漿料的流動性很好,所以在使用過程中,可能出現泌水扒底的現象,本文通過加入改性劑消除壓漿料可能出現的泌水缺陷,并且在改性劑含有使壓漿料硬化漿體產生微膨脹的組分,維持硬化漿體的體積穩(wěn)定性,防止出現收縮現象。確定的改性劑的摻量為1.8%。 3.2.2 優(yōu)化后的壓漿料性能 在壓漿料基本組分研究的基礎上,經優(yōu)化后的壓漿料的最終配合比見表3.3。 表3.3優(yōu)化后的壓漿料的配合比(wt.%)
表3.4壓漿料的性能
由壓漿料的性能測試結果可以看出,經優(yōu)化后的壓漿料的各項指標均符合《鐵路后張法預應力混凝土梁管道壓漿》的要求,并且無泌水、扒底現象,硬化漿體表面光滑、美觀。 結論 針對目前現有壓漿料存在的流動性差及早期強度低等問題,研究了高效聚羧酸減水劑及早強劑對壓漿料性能的影響,并利用消泡劑、改性劑和塑性膨脹劑對壓漿料的性能進行改善,得到壓漿料的最優(yōu)配合比,并測試了相關性能。結論如下: 1、適宜的減水劑摻量有利于壓漿料流動度的改善。在壓漿料中加入早強劑甲酸鈣有助于壓漿料早期力學性能的發(fā)揮,并且改善凝結時間。引入摻合料粉煤灰,不僅可以達到利用工業(yè)固體廢棄物的目的還能適當改善壓漿料的性能 2、經優(yōu)化后的壓漿料的配合比為:水泥79.5%,粉煤灰15%,減水劑1.0%,早強劑2.5%,消泡劑0.2%,改性劑1.8%,具有高流態(tài)、早強、高強、不泌水、無收縮的壓漿材料。改善了壓漿材料存在著強度、流動性差,泌水,干燥收縮出現裂縫等缺陷。凸顯出其強度高、流動性強、早期塑性膨脹明顯、損失較小等優(yōu)勢,與此同時,真正達到了工作性能、強度與早期膨脹性協(xié)調發(fā)展的理想化效果。該壓漿料有望于在鐵路后張預應力混凝土橋梁管道的壓漿處理中得到實際應用,這對提高混凝土橋梁的結構耐久性和使用年限將會起到極大的積極作用。